A mechanical seal with a sliding velocity
greater than 25 m/s, such as is found e.g. in high-speed pumps, compressors and gas
turbines. Typical features of a mechanical seal of this type are its stationary spring backing, rotating counter
ring and an optimized coolant guide system. Fallowing factors must be observed when
designing a high-speed seal:
- Spring backing: Starting from around 25 m/s, stationary springs are employed to
ensure adequate buckling strength. In the intermediate
range up to about 35 m/s it is possible to use revolving multiple springs with a spring guide.
- Power consumption: The mechanical seal's overall power consumption is the sum total of
the power consumption, rather: friction loss which
increases as a linear function of the speed n, and of the turbulence
losses (from the liquid's friction between the rotating parts of the mechanical seal
and the seal casing), which increase by the function n2.8 and begin to exert
distinctly more influence from around 30 m/s. This explains why it is necessary to
minimize the maximum diameter of seals of this type, to select high-wear-resistant face
materials with high thermal conductivity (preferably silicon
carbide/ tungsten carbide running against antimony-impregnated carbon graphite), and to make provision
for intensive cooling of the seal.
- Coolant guide system: Temperature-related differences in density may restrict the
exchange of coolant directly at the sealing gap, causing an obstruction of heat
dissipation around the rotating parts of the seal. Positive guidance of the coolant (using
flow guides) proves beneficial. The coolant itself must
display the lowest possible viscosity and minimum gas
solvent power, as the dissipation of heat at the sealing gap can also be obstructed by any
gas ring formed when gas components are released due to the given rise of temperature with
concurrent drop of pressure. With oils it is important to consider which additives are
used, as any deposits on the sliding faces can cause the
gap to expand and hence the leakage to increase. As a
general rule preference should be given to coolants that leave no or as little residue as
possible when they evaporate.
- Freedom from unbalance, reduction of vibration: The high balance qualities usually
demanded for high-speed machines force manufacturers to apply closer production and
running tolerances. Rotating masses must be kept as small as possible, and the machine
manufacturer has to be consulted to check whether it is necessary to balance the seal. The
main dangers for high-speed seals lie in the appearance of thermal
stress cracks on the mostly carbide seal faces, in unacceptable thermal warping of the seal faces themselves, in overshooting of the
pressure-dependent boiling points in the area of the sliding faces with subsequent dry running, and in the formation of deposits on the seal faces with a subsequent unacceptable
increase of leakage
|
|
Typical examples of double high-speed
seals
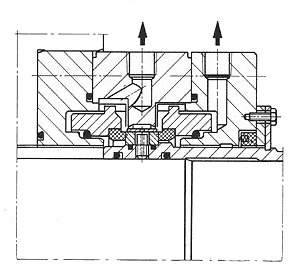
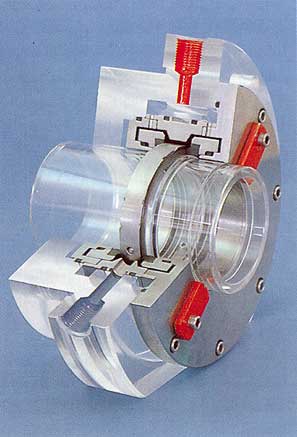
|